GLOSSARY OF
Common Drilling Fluids Management Terms
Confused by the complex jargon of drilling fluids management?
Let The Panther Companies’ Glossary of Common Drilling Fluids Management Terms be your guide!
Compiled by industry experts, our comprehensive glossary is designed to enhance your understanding of the most prevalent terms in the oil and gas industry. From drilling additives and chemicals to types of drilling muds and fluids management practices, our guide has you covered.
Take your drilling fluid expertise to the next level today. Download your free PDF version today!
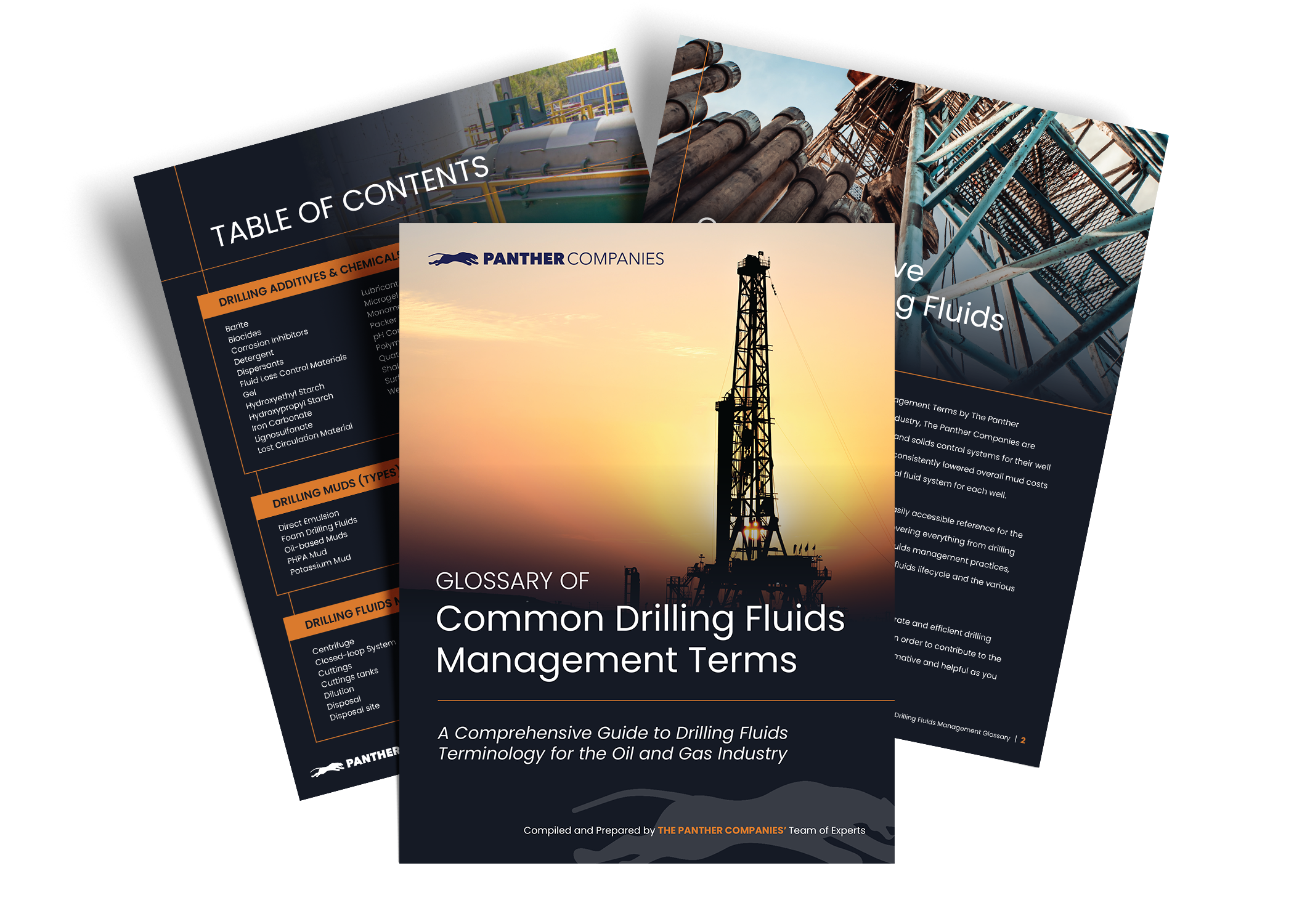
Welcome to the Glossary of Common Drilling Fluids Management Terms by The Panther Companies. With years of experience in the oil and gas industry, The Panther Companies are dedicated to helping clients determine the best additives and solids control systems for their well operations. Our comprehensive drilling fluid systems have consistently lowered overall mud costs for clients, and our customized approach ensures the optimal fluid system for each well.
This glossary is designed to provide you with a concise and easily accessible reference for the most common terms related to drilling fluids management. Covering everything from drilling additives and chemicals to various types of drilling muds and fluids management practices, this glossary aims to enhance your understanding of the drilling fluids lifecycle and the various contingencies that may arise based on well conditions.
At The Panther Companies, we understand the importance of accurate and efficient drilling fluid management, and we are committed to sharing our expertise in order to contribute to the success of your operations. We hope you find this glossary both informative and helpful as you navigate the complex world of drilling fluids management.
TABLE OF CONTENTS
Barite
Biocides
Corrosion Inhibitors
Detergent
Dispersants
Fluid Loss Control Materials
Gel
Hydroxyethyl Starch
Hydroxypropyl Starch
Iron Carbonate
Lignosulfonate
Lost Circulation Material
Lubricant
Microgel
Monomer
Packer Fluid
pH Control Agents
Polymers
Quaternary Amine
Shale Inhibitor
Surfactants
Weighting Agents
Direct Emulsion Foam
Drilling Fluids
Oil-based Muds
PHPA Mud
Potassium Mud
Silicate Mud
Synthetic-based Muds
Water-based Muds
Centrifuge
Closed-loop System
Cuttings
Cuttings tanks
Dilution
Disposal
Disposal site
Drying Shakers
Haul Off
Rheology
Rig Shaker
Solids Control
Viscosity
DRILLING ADDITIVES & CHEMICALS
In this section, we’ll dive into the world of essential chemicals and materials that keep drilling operations running smoothly. These additives are the secret sauce that enhance drilling fluid properties and make sure everything works as it should. Here, you’ll find easy-to-understand definitions for all sorts of additives, from popular weighting agents to specialized corrosion inhibitors and more, giving you a solid grasp of their roles and benefits in the oil and gas industry.
BARITE
Barite is a mineral composed of barium sulfate commonly used as a weighting agent in oil and gas drilling fluids. By increasing the density of the mud, barite provides enough weight to counteract the upward pressure of formation fluids, preventing well blowouts and enabling more accurate well control when drilling through pressurized zones.
BIOCIDES
Biocides are chemical additives that control microbial growth, such as sulfate-reducing bacteria, slime- forming bacteria, and
iron-oxidizing bacteria, in drilling fluid systems. They help prevent contamination, corrosion, and the formation of unstable fluid properties, and are commonly used in water-based muds containing natural additives susceptible to bacterial attack.
CORROSION INHIBITORS
Corrosion inhibitors are chemical compounds that safeguard metal surfaces, such as those found in drilling equipment and pipelines, from corrosive compounds present in their environment. These inhibitors function by creating a protective barrier on the exposed metal surface, which prevents contact with corrosive elements. As a result, the corrosion rate is significantly reduced, leading to an extended equipment lifespan and decreased maintenance costs. This protective mechanism is essential for the preservation of various industrial assets and infrastructure components.
DETERGENT
Detergents are cleaning agents commonly used in the oil and gas industry to remove dirt, oil, and other contaminants from drilling equipment and surfaces. They are typically added to the upper-holes drilling fluid, where they function to reduce surface tension and minimize bit and Bottom Hole Assembly (BHA) balling. This results in improved drilling efficiency and a reduced likelihood of formation damage. Additionally, detergents can act as emulsifiers and have the ability to reduce torque and drag without the need for oil additions in the system. Their versatile properties make them an essential component in maintaining optimal drilling performance and equipment longevity.
DISPERSANTS
Dispersants, or thinners, are chemical compounds employed to regulate the rheology of drilling mud by reducing its gel strength.
Lignite, desco, and lignosulfonate are common types of dispersants used in the oil and gas industry. These dispersants help maintain well control and boost drilling efficiency by preventing the settling of solids such as clay, sand, and silt. They function by breaking down particles into smaller sizes and diminishing surface tension between the particles and the fluid, enabling them to remain suspended in the drilling mud. This process is essential for ensuring optimal drilling performance and wellbore stability.
FLUID LOSS CONTROL MATERIALS
Fluid Loss Control Materials are specialized additives used in drilling operations to manage and minimize the loss of drilling fluid into the formation. These materials, such as natural, biodegradable polysaccharides like starch, are derived from plants and help control fluid loss, improve viscosity, and provide filtration control. By forming a low-permeability filter cake on the wellbore wall, these materials effectively prevent excessive fluid invasion into the formation. Some starches can be chemically modified, resulting in derivatives like hydroxyethyl starch and hydroxypropyl starch, which offer enhanced properties and effectiveness in various drilling conditions.
GEL
A gel is a type of drilling fluid additive composed of clay material, primarily Montmorillonite (MMT), with bentonite being a natural example. It is used to provide lubrication and cooling during the drilling process. When added to the drilling fluid, its primary function is viscosity and filtration control, but it also offers various benefits, including lubrication and cooling the drill bit. Gels help stabilize the wellbore, maintain a specific viscosity for transporting cuttings and drilling mud to the surface, and provide advantages over traditional drilling fluids. These advantages include better lubrication, enhanced drilling efficiency, and a reduced environmental impact.
HYDROXYETHYL STARCH
Hydroxyethyl starch is a nonionic starch derivative, functionally analogous to hydroxyethylcellulose (HEC) in its method of manufacture and most applications for drilling, workover, and completion fluids. Rather than using a cellulosic starting material, such as HEC, starch is used instead and reacted with ethylene oxide in an alkaline environment. This synthetic, water-soluble polymer is employed as a thickening agent in drilling fluids to enhance viscosity, lubrication, and well control. Derived from natural starches like cornstarch, hydroxyethyl starch is more biodegradable and environmentally friendly compared to some alternative options.
HYDROXYPROPYL STARCH
Hydroxypropyl starch (HPS) is a synthetic, water-soluble polymer used to increase drilling fluid viscosity, helping to maintain borehole stability and control cuttings flow. Derived from natural starches, HPS offers higher gel strength and greater resistance to degradation than hydroxyethyl starch, making it suitable for high-temperature, high-pressure drilling operations.
IRON CARBONATE
Iron carbonate is a non-toxic, non-metallic mineral used as a weighting agent in drilling fluids to counteract the upward pressure of formation fluids and prevent well blowouts. Often used as an environmentally friendly alternative to barite, iron carbonate can also be used as a filler in drilling muds and in the construction of drilling rig foundations.
LIGNOSULFONATE
Lignosulfonate is a natural polymer derived from wood pulp used as a viscosifying agent in drilling fluids. Stable under high-temperature and high- pressure conditions, lignosulfonates help maintain fluid stability, reduce fluid loss, and increase filter cake efficiency.
LOST CIRCULATION MATERIAL
Lost circulation materials (LCMs) are specialized additives used in drilling fluids to seal off fractures, fissures, or permeable formations, preventing the loss of drilling fluid into the formation. LCMs can be fibrous, granular, or flake-like, and may include materials like ground nutshells, mica, or graphite.
LUBRICANT
Lubricants are additives used in drilling fluids to reduce friction between the drill string and the wellbore, decreasing wear and tear on equipment and improving drilling efficiency. They can be oil- based, water-based, or synthetic and are essential for optimal drilling performance.
MICROGEL
Microgels are small, cross-linked polymer particles that can swell in the presence of water, functioning as a viscosifying and suspending agent in drilling fluids. They help maintain borehole stability, control fluid loss, and reduce fluid filtration.
MONOMER
Monomers are small, single molecules that can chemically bond together to form larger, more complex structures called polymers. In the context of drilling fluids, monomers serve as building blocks for creating both synthetic and natural polymers that fulfill various functions, such as viscosity control and fluid loss reduction. Polymers such as starch, guar gum, and xanthan gum are examples of natural polymers derived from monomers that are utilized in the oil and gas industry to enhance drilling fluid properties and improve overall drilling performance.
PACKER FLUID
Packer fluid is a specialized drilling fluid used to isolate and protect the annular space between the casing and the production tubing. It provides hydrostatic pressure, minimizes corrosion, and prevents the passage of formation fluids or gases.
PH CONTROL AGENTS
pH control agents are chemical additives used in drilling fluids to regulate pH levels, ensuring optimal performance of other fluid components and minimizing potential formation damage. Common pH control agents include lime, soda ash, and caustic soda.
POLYMERS
Polymers are large, chain-like molecules made up of repeating units called monomers. In drilling fluids, polymers can serve various functions, such as viscosifying, fluid loss control, and shale stabilization, depending on their chemical structure and properties.
QUATERNARY AMINE
Quaternary amines are a class of chemical compounds used as biocides, surfactants, and shale inhibitors in drilling fluids. They are effective in controlling bacterial growth, reducing surface tension, and inhibiting clay swelling, respectively.
SHALE INHIBITOR
Shale inhibitors are additives used in drilling fluids to prevent wellbore instability and minimize formation damage by inhibiting the swelling and dispersion of shale particles. These additives stabilize the shale formations by reducing the interaction between drilling fluid and reactive clay minerals.
SURFACTANTS
Surfactants are chemical additives used in drilling fluids to reduce surface tension, enhance lubrication, and emulsify oil and water phases. They improve the wetting properties of drilling fluids, facilitating the removal of drilled cuttings and reducing the potential for formation damage.
WEIGHTING AGENTS
Weighting agents are dense, inert materials added to drilling fluids to increase their density, counteracting the pressure of formation fluids and preventing well blowouts. Common weighting agents include barite, iron carbonate, and hematite.
DRILLING MUDS (TYPES)
Drilling muds play a crucial role in wellbore stability, carrying cuttings to the surface, and controlling downhole pressures. In this part of the glossary, we’ll explore the different types of drilling muds used in the oil and gas industry. You’ll find straightforward definitions for a variety of drilling muds, from oil-based and synthetic-based to water-based and specialized mud systems. Get ready to expand your knowledge on the diverse world of drilling muds and their unique applications in the field.
DIRECT EMULSION
A direct emulsion is a type of oil-based drilling fluid in which oil droplets are suspended within a continuous water phase. This emulsion is designed to address various drilling challenges, such as lubrication, stuck pipe, formations with fracture gradients less than water, and inhibiting salt formations to minimize washout. By providing improved lubrication, reduced fluid loss, and enhanced stability, direct emulsions are particularly beneficial in high-temperature and high-pressure drilling environments. These properties contribute to increased drilling efficiency, better wellbore stability, and reduced formation damage.
FOAM DRILLING FLUIDS
Foam drilling fluids are gas-liquid mixtures formed using a blend of air, water, and a surfactant, often utilized in air drilling operations. These fluids are commonly used in areas where formations are dry and provide wellbore stability, minimize fluid loss, and enhance cuttings removal. Foam drilling fluids are particularly suitable for drilling in formations with low fracture gradients, unstable shales, or lost circulation zones, offering a more efficient and environmentally friendly alternative to traditional drilling fluids in specific drilling conditions.
OIL-BASED MUDS
Oil-based muds (OBMs) are drilling fluids that use oil as the continuous phase, helping to maintain borehole stability, lubricate the drill string, and suspend cuttings for removal. They are often used in high- pressure and high-temperature environments due to their excellent thermal stability.
PHPA MUD
PHPA mud is a water-based drilling fluid that contains partially hydrolyzed polyacrylamide (PHPA), a polymer used to encapsulate drill cuttings and inhibit clay hydration. PHPA muds help control fluid loss, minimize shale swelling, and reduce the potential for formation damage.
POTASSIUM MUD
Potassium mud is a water-based drilling fluid containing potassium ions, which interact with clay minerals in the formation, preventing swelling and stabilizing the wellbore. These muds are particularly useful when drilling through reactive shale formations.
SILICATE MUD
Silicate mud is a water-based drilling fluid containing sodium or potassium silicate, which helps control shale hydration, stabilize the wellbore, and minimize formation damage. Silicate muds provide improved wellbore stability in reactive clay formations and are environmentally friendly.
SYNTHETIC-BASED MUDS
Synthetic-based muds (SBMs) are drilling fluids that utilize synthetic oil as the primary fluid component, offering a balance between environmental compatibility and performance advantages. They provide good lubrication, shale stability, and wellbore cleaning properties, while reducing the environmental impact compared to conventional oil-based muds.
WATER-BASED MUDS
Water-based muds (WBMs) are drilling fluids that use water as the continuous phase, with various additives mixed in to optimize drilling performance. They are generally more environmentally friendly and cost-effective than oil-based or synthetic-based muds but may have limited effectiveness in certain drilling conditions.
DRILLING FLUIDS MANAGEMENT
Efficient drilling fluids management is vital for maintaining operational integrity, minimizing environmental impact, and ensuring cost-effectiveness. In this section, we’ll dive into the terminology related to practices and equipment that help manage drilling fluids in the oil and gas industry. Here, you’ll find easy-to-understand definitions for various terms, from solids control techniques and equipment like centrifuges and rig shakers to disposal methods and rheology. This compilation of terms is designed to enhance your understanding and appreciation of the critical role drilling fluids management plays in the overall success of drilling operations.
CENTRIFUGE
A centrifuge is a mechanical device used in drilling fluid management to separate suspended solids, including drill cuttings, from the fluid by rotating at high speeds. This process helps maintain the fluid’s properties and minimizes waste generation.
CLOSED-LOOP SYSTEM
A closed-loop system is a drilling fluid management approach that minimizes waste by recirculating and reusing drilling fluids throughout the drilling process. This system reduces the environmental impact and can result in cost savings by minimizing fluid consumption and disposal.
CUTTINGS
Cuttings are small pieces of rock and sediment generated during drilling, which are brought to the surface by the drilling fluid. They need to be separated from the fluid and managed properly to maintain drilling efficiency and minimize environmental impact.
CUTTINGS TANKS
Cuttings tanks are containment vessels designed to store drill cuttings after they have been separated from the drilling fluid. These tanks provide temporary storage before the cuttings are either treated for reuse or transported for disposal.
DILUTION
Dilution is the process of adding clean base fluid, water, or oil to a drilling fluid system to reduce its viscosity, lower the concentration of solids, or adjust its chemical properties. Dilution is a common solids control technique used to maintain the optimal performance of drilling fluids.
DISPOSAL
Disposal refers to the process of safely and responsibly discarding drilling
waste, including used drilling fluids and drill cuttings. This can involve onsite treatment, transport to a designated disposal site, or other methods in compliance with environmental regulations.
DISPOSAL SITE
A disposal site is a designated location where drilling waste, such as used drilling fluids and cuttings, can be safely and responsibly discarded in compliance with environmental regulations and industry standards.
DRYING SHAKERS
Drying shakers are vibrating screens used to separate drilling cuttings from drilling fluids, helping to remove excess fluid and reduce the volume of waste material. By reducing the amount of fluid retained by cuttings, drying shakers can improve waste management efficiency and minimize disposal costs.
HAUL OFF
Haul off is the process of transporting drilling waste, such as drill cuttings and used drilling fluids, from the drilling site to a designated disposal site for proper treatment or disposal in compliance with environmental regulations.
RHEOLOGY
Rheology refers to the study of the flow and deformation behavior of drilling fluids, which is important for optimizing fluid properties to maintain borehole stability, transport cuttings, and minimize formation damage during drilling operations.
RIG SHAKER
A rig shaker is a vibrating screen device, typically located on a drilling rig, that separates drill cuttings from drilling fluids as they return to the surface. This separation process helps maintain drilling fluid properties and minimizes waste generation.
SOLIDS CONTROL
Solids control is the process of removing unwanted solid particles, such as drilled cuttings and formation debris, from drilling fluids to maintain their desired properties and minimize the potential for wellbore instability, equipment wear, and formation damage. Solids control techniques include dilution, mechanical separation, and chemical treatment.
VISCOSITY
Viscosity is a measure of a fluid’s resistance to flow or deformation, which is an important property in drilling fluids. Optimal viscosity allows drilling fluids to effectively transport cuttings, maintain borehole stability, and reduce fluid loss to the formation.